A “Smart” Self-monitoring composite tool for aerospace composite manufacturing using Silicon photonic multi-sEnsors Embedded using through-thickness Reinforcement techniques
[January 2020 – December 2023]
PCRL coordinated the SEER Project. SEER was an Innovation Action that aimed to develop smart self-monitoring composite tools, capable of measuring process and material parameters and, thus, providing real-time process control with unprecedented reliability. The SEER consortium achieved this by:
- developing miniature photonic sensors,
- embedding those sensors in the tool using through-the-thickness techniques that minimized alteration of the tool’s structural integrity, and
- optimizing the manufacturing control system through the implementation of a prototype process monitoring, optimization, and process control unit.
SEER adopted a multi-sensor approach that comprised a temperature, refractive index, and pressure sensor, all operating in the near-infrared and integrated on a miniature photonic integrated circuit (PIC). The SEER solution was compatible with and optimized existing composite manufacturing methods. Its reuse for several resin curing cycles increased efficiency and saved resources. The embedded PIC sensors in a reusable tool addressed preprocessing challenges and used acquired raw data for process optimization through theoretical models and machine learning algorithms. This established a link between sensor data, material state models, process parameters, and tool degradation for each tool.
This approach enabled efficient preventive maintenance with minimal effort and provided insights for better tool design. Finally, the acquired data from quality testing of cured parts optimized process control, enhancing quality yield and providing a part quality fingerprint.
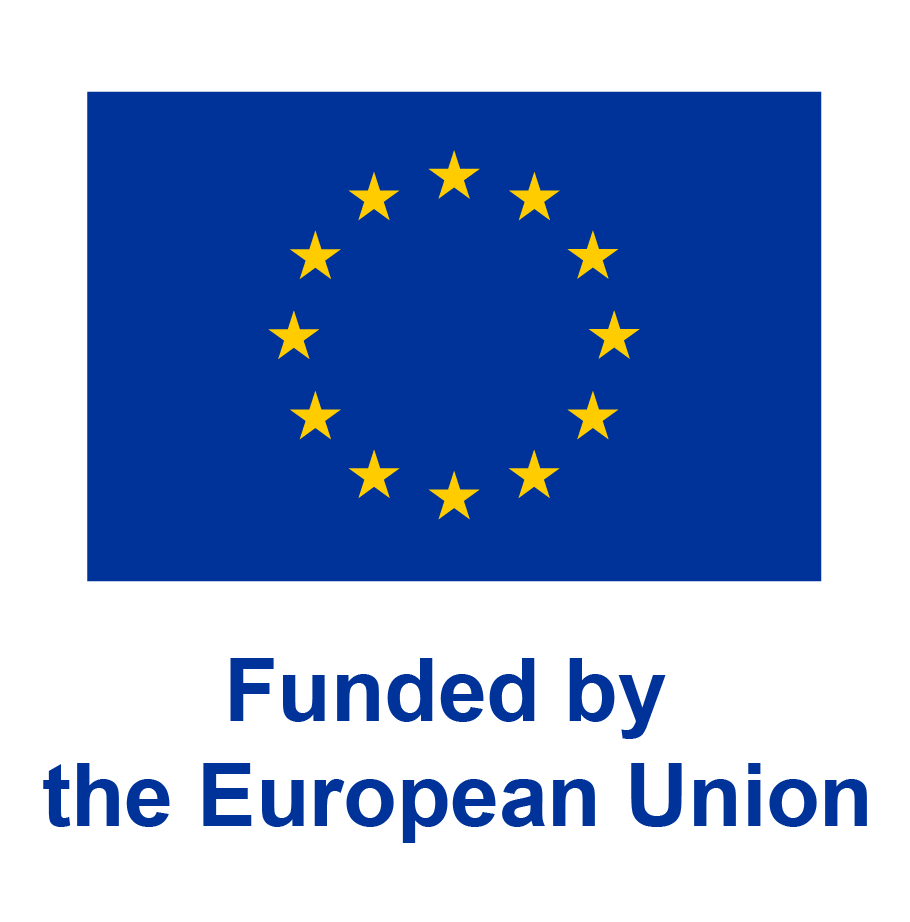